SIXBAU Roof
nailed plate roofSIXBAU Roof prefabricated roof structures offer a fast and perfect solution compared to traditional carpentry roof structures, while guaranteeing uncompromising quality. Factory-made SIXBAU Roof roofs can be assembled on site in as little as one day, making work easier, significantly reducing construction time and costs. SIXBAU Roof roof structures are made of KVH wood shipped from Austria and made on precise Swedish Randek machines. Based on the digital designs of the dreamed roof structure, the production of corner roofs is carried out with a high degree of precision under continuous quality control. The proper fire protection of the finished roof structure, as well as the resistance of mold, fungi and insects, is ensured by the chemical treatment of the wooden supporting elements. The finished SIXBAU Roof roof structures can be assembled quickly and easily on site without further repairs.
Roof
nailed plate roofFor the construction of roof structures for residential, community, industrial and other buildings. Download price list.
The manufacturing process of the roof structure
1. USE OF QUALITY RAW MATERIALS
Our nailed roof structures are made exclusively from raw materials certified by KVH, C24 grade CE15 EN15497 from Austria. Our nailed plates used in the manufacture of our roofs are CE-certified nails made of high-strength, 1.5 mm thick hot-dip galvanized sheet steel. The sheer appearance of the raw materials we use is also significantly different from the roofing materials commonly used in the construction industry.
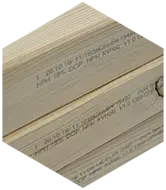
2. CUTTING ON THE BASIS OF DIGITAL DESIGNS WITH SWEDISH RANDEK TECHNOLOGIES
Computer-controlled, Swedish Randek-type cutting machines, programmed according to the designs of the ordered roof, produce the components of the designed roof with amazing precision, which are inspected and marked according to the assembly drawing.
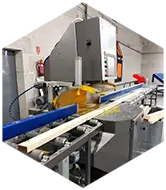
3. SURFACE TREATMENT AND PROTECTION FOR EVEN BETTER DURABILITY
After cutting, the marked roof elements are treated with a CE-certified special wood preservative with immersion technology, thanks to which the preservative perfectly surrounds and penetrates the wood materials, thus ensuring the protection of the future roof structure against mold, fungi and insect damage. The wood thus treated is ready for assembly after drying.
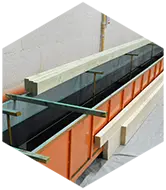
4. ASSEMBLY PRESSING AND INSPECTION IN PRECISE
The roof structure brackets are assembled on magnetic benches with millimeter accuracy and continuous quality control. Based on the size and position in the assembly drawing, all structural elements are placed, which are then fastened together on both sides of the holder with CE-quality nailed plates pressed simultaneously with a hydraulic press providing a pressure of 150 bar. During the manufacturing process, the nailed beams remain horizontal throughout, so the wooden elements that are fastened to each other cannot move or twist. After pressing, the brackets are subjected to a final quality control, which completes the production process.
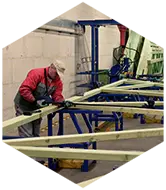
5. PROVEN QUALITY FROM FIRST STEP TO THE LAST
Our production plant has a multi-stage ÉMI-certified in-production control system, which accompanies the entire production process, as evidenced by our CPR code. If everything is in order, we place the appropriate markings on the brackets. (CE marking, markings according to the assembly drawing, project identification and the required level of on-site polystyrene concrete pouring are marked with a red bar.)
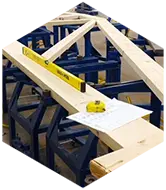
6. PREPARATION FOR SHIPMENT
The finished pre-assembled brackets are grouped by size and strapped for stable, safe transport. The components of the manufactured roof structure will be stored in a covered hall designated for the project until delivery. For each roof, a roof structure design documentation and a declaration of performance are issued after the final inspection. Based on the roof construction plan, properly marked elements can be easily identified and the roof can be assembled easily and quickly on site.
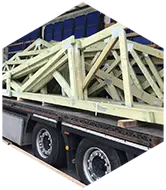